EXPERIENCE

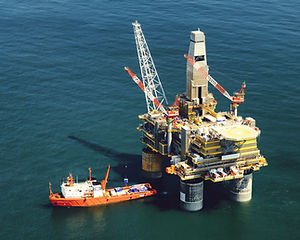
Maersk Oil Qatar
We undertook production optimization initiatives to enhance the forecasting process within the organization. Our objective was to align anticipated deliveries and create a cohesive priority framework. The successful execution of the forecasting process was supported by the incorporation of an Activity Planning Process.
Additionally, we developed the MPP & Choke process, which played a crucial role in establishing and final choke models for all hydrocarbon streams, including water injection and condensate. We also created a method to identify and analyze unplanned and potential losses within the business. In the initial phase, we implemented short-term optimization strategies and integrated them into the Critical Weekly Events (CWE) framework, outlining key meetings related to Shutdowns (STO) and loss management.
These efforts culminated in total savings exceeding $12.6 million.

Mid-Stream Sour Gas Plant
An Operations Excellence project was successfully executed at a Mid-Stream gas processing facility, aimed at improving pricing, throughput, and the recovery of C3+ components.
This success was achieved through a comprehensive strategy that included debottlenecking, careful programming, and the optimization of key operational and technical processes. Significant enhancements in critical equipment uptime were also realized, along with improvements in the contract review process and communication among Operations, Maintenance, the Plant, and Head Office.
To ensure the lasting impact of these outcomes, we developed and implemented an Integrated Performance Management System, which included effective tools for Production Loss Accounting and CAPEX Project Prioritization.
The project resulted in annual savings exceeding $14 million, surpassing the initial business case by an impressive 40%.

Ecopetrol Colombia
A successful Operations Excellence project was implemented at a Colombian refinery, yielding impressive results. The main objective was to optimize throughput across the refinery's 12 unique plant areas, leading to enhanced production output.
With over 1,500 personnel on-site, the project was spearheaded by six committed team members and divided into four workstreams. This initiative significantly improved the facility's operational efficiency, particularly increasing run rates. By streamlining management and control processes and promoting behavioral changes, the sustainability of these enhancements was ensured.
The project generated significant annual savings, surpassing $40 million in total.
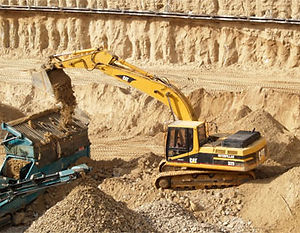
Teck Mining Chile
A highly successful Plant Maintenance project focused on improving maintenance and reliability processes delivered outstanding results.
Key include a significant boost in equipment reliability, rising from 58% to an impressive 84%. Resource utilization was also optimized, increasing from 71% to a strong 87%. This initiative resulted in a notable reduction in maintenance costs, with estimated savings of around $8 million.
Additionally, the project to minimize downtime during shutdowns for plate changes on the SAG Mill and Ball Mill, which previously exceeded 100 hours. Our efforts successfully reduced the cycle time for the SAG Mill by 34 hours and the Ball Mill by 54 hours, leading to overall savings estimated at $6.2 million.